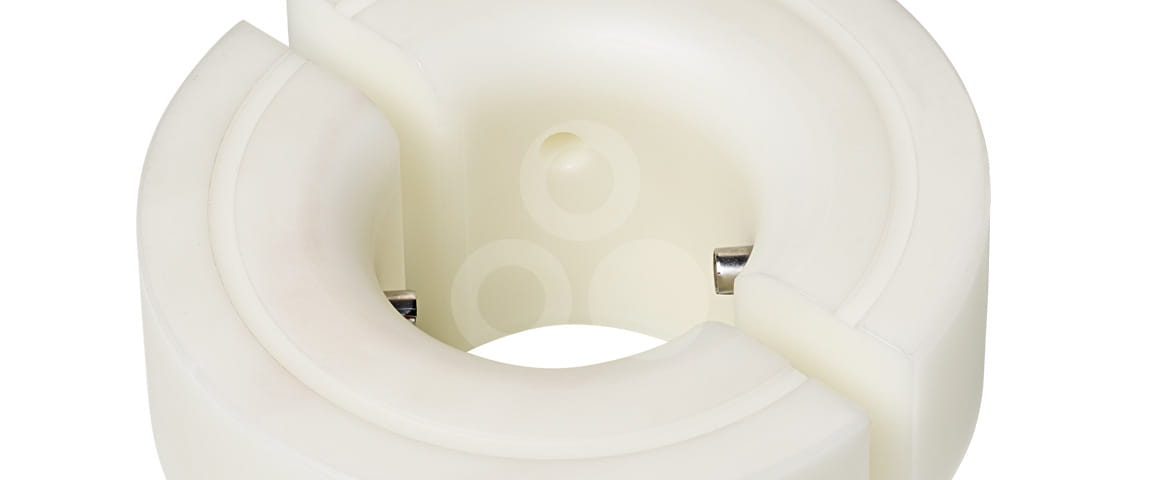
Hydrophone housings in seismic surveys
In the field of oil and gas exploration, seismic surveys are performed to locate and determine the size of oil and gas pockets. The most common technique used to determine possible deposits is using highly sensitive hydrophones. Hydrophone strings consist of thousands of linked individual hydrophones, encased in lubricant filled tubing. These hydrophones are used to record sound waves that are bounced off the ocean floor, which provide information on rock formations and possible deposits.
Requirements in harsh environments
Before any oil drilling can take place, possible oil wells must be located. On average, only about one in every ten wells are successful, making it imperative that the information recorded by the individual hydrophone is accurate. All aspects of the hydrophones must be highly reliable and unhindered by any faults to avoid misleading readings, reducing further costly exploration and minimizing the environmental impact. To ensure this, the individual hydrophones require housings to protect them from damage. Engineering materials such as metals, ceramics and plastics are typically used to construct the hydrophone housings. Key factors must be considered when choosing the material for this application, as the environment that it operates in poses a number of obstacles which could cause potential damage. Saltwater, sunlight and chemicals such as oils and lubricants used within the tubing can have an impact on the operation of the hydrophones, therefore good chemical resistance is paramount. Other factors such as impact resistance, dimensional stability and acoustic properties should also be considered.
Innovative solutions
Engineering thermoplastics are highly advantageous for these housings given the exceptional properties that they hold. Metals tend to be far heavier than plastics, therefore the use of plastics would be particularly beneficial on ships, where weight and ease of handling a lighter material is favored. Ceramics are usually more expensive than plastics, harder to machine and damage easily due to their brittleness.
Profit from saving costs and time
The use of plastics can lead to longer part lifetime in comparison to brittle ceramics, thus, resulting in reduced maintenance, downtime due to damages or faulty readings, and replacements costs. In addition to this, these thermoplastics, in particular TECAFORM AD, have great machinability saving time and reducing costs.
Furthermore, Ensinger has a broad portfolio of thermoplastics ideal for this application, each holding properties to suit your special requirements. Alongside this, Ensinger's team of technical application engineers are on hand to advise you with material selection in order to provide the optimum solution for your application.