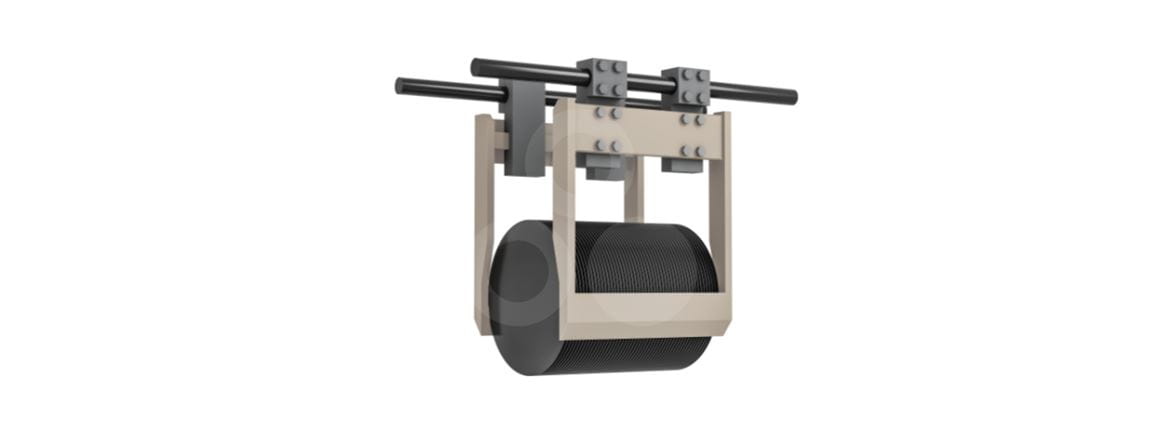
Wet Bench Wafer Holder
Strength, chemical resistance, and copy exact for wafer mobility parts
PEEK enables highest level of wafer position accuracy
In this case study, the shape TECAPEEK SX natural, semiconductor grade unfilled PEEK, has been selected for a wet bench wafer holder. The function of the wafer holders is to dip multiple wafers into several chemical processing baths. The PEEK parts are holding the wafers from the sides to allow the liquid chemicals unobstructed access to the wafers when inserting to the bath. The number of wafers being held is maximised to enhance better wafer throughput, while maintaining sufficient and consistent spacing between the wafers to allow the liquids to pass through. The material must be highly dimensional stable to maintain the tight tolerances of the slot pitch spacing, thus maintain the wafer position accuracy. Moreover, the material needs to provide elevated levels of strength and rigidity, as well as wear resistance to maintain dimensional accuracy and maximise part lifetime under high wafer load and hundreds of thousands of cleaning cycles. PEEK fulfills the requirements for dimensional stability over an extended period due to high stiffness and creep resistance, as well as low water absorption. PEEK offers an excellent combination of elevated mechanical properties with a high level of chemical resistance.
You can take a closer look at Ensinger's wet bench wafer holder made of TECAPEEK SX by zooming and rotating here:
TECAPEEK SX natural – the perfect match
Chemical resistance at room temperature
Chemical |
Formula |
Concentration [%] |
PI |
PEEK |
PPS |
PEI |
PVDF |
PTFE |
PET |
POM-C |
Deionized water | H2O | - | + | + | + | + | + | + | + | + |
Hydrofluoric | HF | 50 | - | + | - | + | (+) | - | - | |
Sulfuric acid | H2SO4 | 95-97 | - | - | + | - | + | (+) | - | - |
Hydrogen peroxide | H2O2 | 30 | - | + | + | (+) | + | + | + | (+) |
2-propanol (isopropanol, IPA) | CH3CHOHCH3 | 100 | + | + | + | + | + | + | + | + |
Acetone | CH3COCH3 | 100 | + | + | + | (+) | - | + | (+)C | + |
Ethanol | (CH3)OCH3 | 95 | + | + | + | + | + | + | + | + |
Hydrochloric acid | HCI | 37 | - | + | + | + | + | + | - | - |
Ammonia solution | NH3 | 25 | - | (+) | + | + | + | + | ||
Orthophosphoric acid | H3PO4 | 85 | + | + | - | + | + | - | - | |
Nitric acid | HNO3 | 69 | (+) | + | + | - | - | |||
Acetic acid | CH3COOH | 100 | (+) | (+) | + | - | + | - | - |
Comment: + = good, (+) = limited; - = unstable
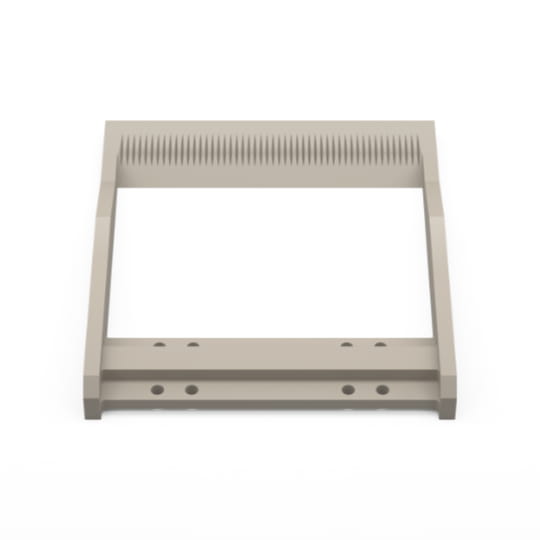
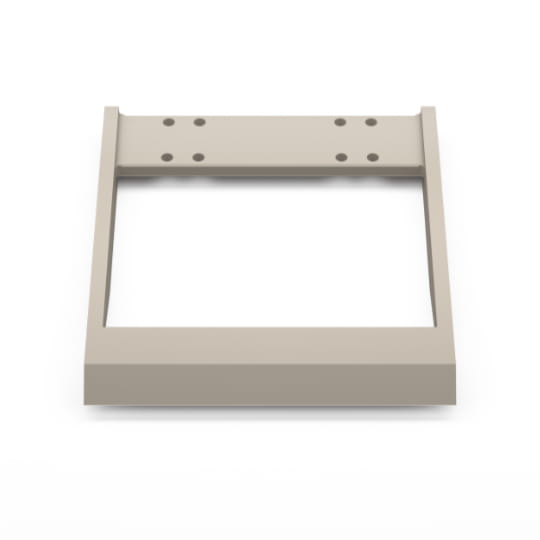