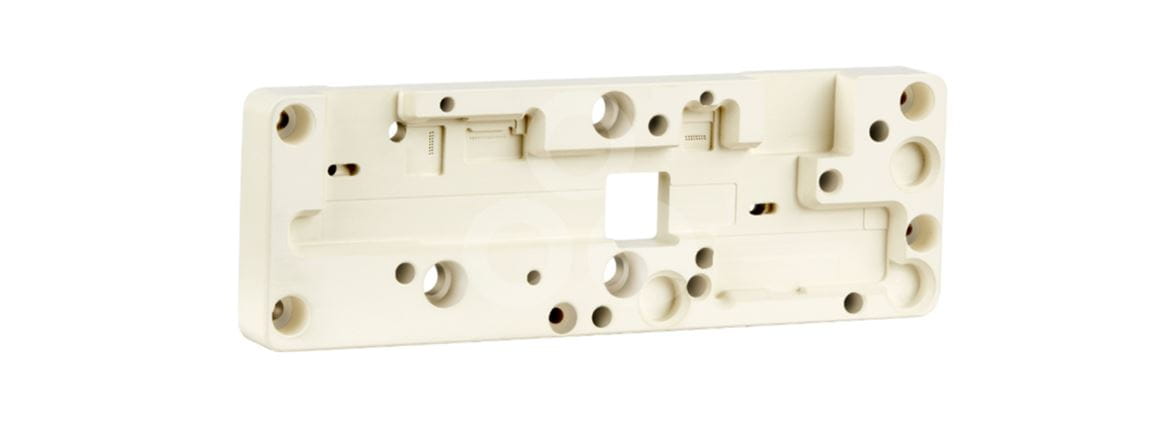
Testing Fixtures for Smartphone Flexible Printed Circuits (FPC) Connectors
As semiconductors and electronic devices are becoming more powerful and complex, the need for reliable functional testing during the manufacturing process is increasing at a rapid pace. Ensinger has decades of experience in supplying high performance plastic materials used in test sockets and testing fixtures for semiconductors and electronic components and has developed specific materials by following the latest market trends and understanding the requirements of these applications. This case study describes how the Ensinger shape TECAPEEK CMF white opened innovative design possibilities for testing fixtures for flexible printed circuits (FPC) connectors used in smartphones.
Materials are challenged by ever-increasing connector miniaturisation
FPCs are increasingly used in electronic devices and smartphone components such as camera modules and antennas as it enables size and weight reductions compared to rigid printed circuit boards. The market is trending towards increased complexity and miniaturisation, with pitch spacing of FPC connector contacts approaching 0,15 mm. As the pitch spacing of the contacts is getting continually smaller, functional testing fixtures must be fabricated with similar small pitch spacing of contact probes. Consequently, the next generation of testing fixtures must utilise special materials that allow machinability of small hole sizes and pitches.
Conventional plastics at its limit
In addition to the requirement of micro-machinability, testing fixtures for FPC connectors must also provide good wear performance and impact strength to withstand testing cycles. Therefore, materials like PAI which provide good wear performance have been commonly used as fixture materials. However, PAI exhibits elevated levels of moisture absorption which induces dimensional changes, so that pin hole tolerances cannot be met. Adding glass fibers to the PAI materials provides slightly reduced moisture absorption, but the fiber reinforcement results in drill bit deflections thus the required micro hole position accuracy cannot be met. Changing the material to unfilled PEEK, PEI, or PPS enables one to eliminate the issue with water absorption, but unfilled PEEK and PEI results in high burr formation and hole position inaccuracy due to its high ductility, while PPS tends to crack and has limited wear resistance.
Water absorption of unfilled plastics
Flexural modulus of unfilled plastics
Tensile elongation of unfilled plastics
TECAPEEK CMF white – the perfect match
TECAPEEK CMF white was selected as the optimum material for FPC connector testing applications. TECAPEEK CMF is a ceramic-filled PEEK with improved stiffness and reduced elongation, enabling minimum burr formation and an elevated level of micro hole position accuracy. The filler system of TECAPEEK CMF white results in much lower drill bit deflection compared to fiber reinforced materials, while realizing similar levels of stiffness. Additionally, TECAPEEK CMF white is produced via an extrusion manufacturing process that offers reduced residual stresses compared to injection molded plates, as well as lower cost than compression molded materials. The reduction in residual stress means there is lower warpage during machining. Outstanding dimensional stability and micro hole machinability enables one to meet the strict tolerances of the latest FCP connector test fixture designs approaching 0,15 mm hole pitches.
TECAPEEK CMF is offering in both white and grey color with same properties.
TECAPEEK CMF is offering in both white and grey color with same properties.
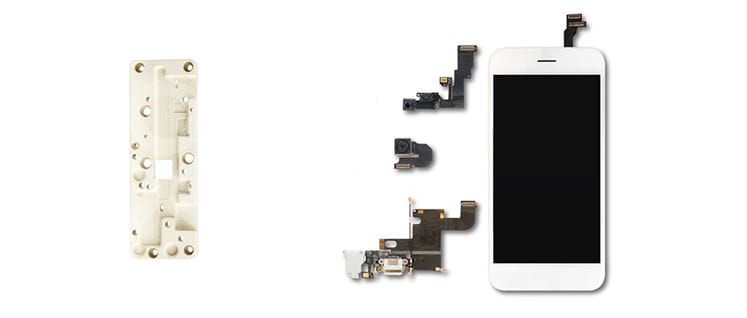
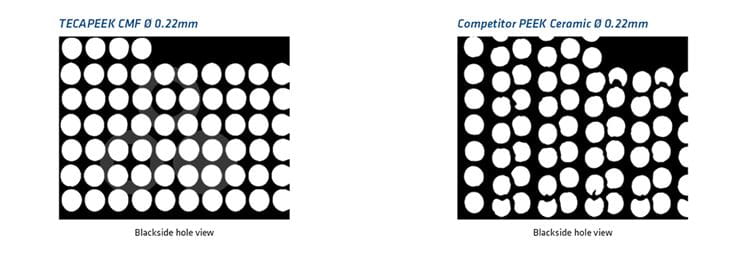