Implants for knee reconstruction
Manufacturers of knee reconstruction products are now in a global market for sales and customers. Apart from the actual implants, tools and instruments, which facilitate handling during the operation, enhance patient safety and can reduce the follow-up expenses for reprocessing. These instruments include test / trial implants, which sometimes serve to differentiate products from the competitors.
The knee joint implant is a polyethylene inlay. Trial implants made of thermoplastic materials like TECASON P MT (the so called UHMWPE inlay) have been used successfully in test implants for years. However, all other test implants - including femur components, tibia components and possibly the shafts - have usually been made of metal.
- However, with metals, there is an increased risk of bioincompatibility. For metals, biocompatibility is only tested and confirmed for the surface alloy. In the event of damage, biocompatibility may thus be forfeited.
- The metal components used up to now have a high dead weight, which may increase the operating expenses during sterilisation: depending on the instrument set, many trays may have to be reprocessed, as the acceptable total weight is soon exceeded with the heavy metal parts.
- Transmission of X-rays would be particularly important for testing the goodness of fit. However, this is impossible with metals.
The future of test implants
The most important requirement is consistent biocompatibility. All our MT plastic semi-finished products are therefore tested in accordance with ISO 10993. Biocompatibility is retained, even if the surface of the plastic test implants is damaged.
The range of Ensinger MT plastics is extended by XRO types (X-ray opaque plastics). By using TECAPEEK MT XRO and TECASON P MT XRO, it is possible to specifically control which parts are visible in the X-ray. This allows the control X-ray to be used to estimate the precision of fit.
There is an extensive colour palette within the MT range, which greatly increases flexibility in designing the test implants. The sizes of the test implants are colour-coded with different colours. This simplifies handling during the operation, as well as measurement of the implant fit on the patient.
Not only can MT plastics be dyed, but also labelled with a laser. Both facilitate branding of the test implants.
The special properties of our high-performance plastics permit creative solutions, even during the design stage. For example, with TECASON P MT, strength and stiffness are ideally balanced. Also, demanding constructional elements such as snap hinge connections can be realised, which is impossible with metal.
Benefits
Strengthening trade name and product branding
Cheap processing and reduced reworking
Long clinical use
MT plastics are very resistant to a variety of sterilisation procedures, such as superheated steam sterilisation, and are also
very resistant to chemicals. This gives test implants that are only made of plastics a very long lifetime in clinical use.
More test implants per tray due to low weight
Safety in product registration
The product registration procedure in the highly
sensitive area of medical devices is often very complex and demanding. During
product development, the biocompatibility test of the semi-finished product
supports the user in risk assessment and improves safety. We also aim to build up and sustain long-term partnerships with our customers and
suppliers. This assures constancy in the
formulation and use. If, however, changes are inevitable, we will of course act
without delay in accordance with a reliable Change Notification Commitment.
Materials for Knee trial implants
TECAPEEK MT
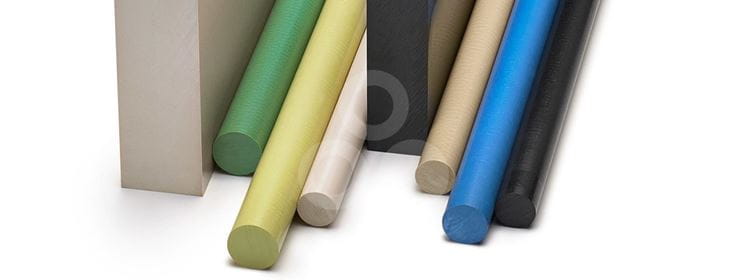
TECASON P MT
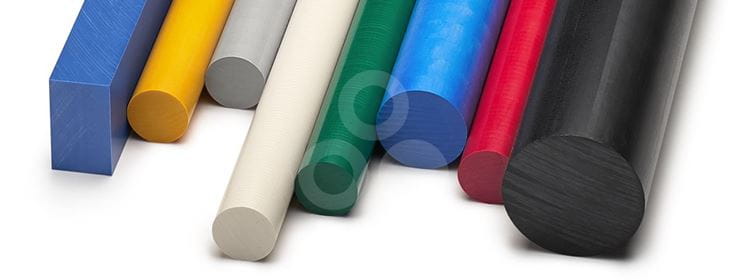
XRO MT materials
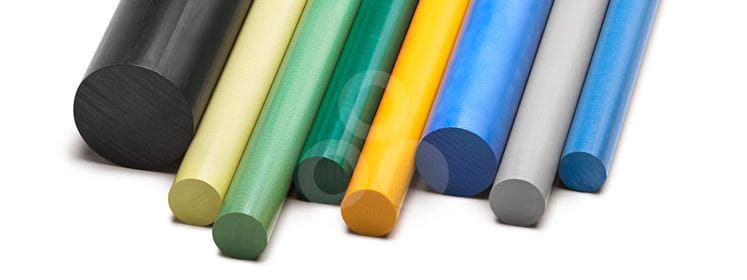