Kompozytowe ramię robota
W tym studium przypadku firmy Loson i Ensinger podjęły współpracę w celu zwiększenia wydajności ramienia robota, które zastosowano w robotach Delta pracujących na automatycznej linii pakowania produktów spożywczych. Te szybkie i precyzyjne maszyny używane są w zakładach do pobierania i pakowania produktów. Dzięki ich szybkości w niektórych przypadkach można uzyskać nawet do 300 pobrań na minutę.
Elementy konstrukcyjne z tworzyw sztucznych wzmocnionych włóknem węglowym (w tym przypadku tkaniną z włókien węglowych z macierzą epoksydową) opracowuje się i produkuje w sposób zapewniający redukcję masy oraz bezwładności przy zachowaniu wysokich parametrów mechanicznych, typowych dla stopów metali o najwyższej jakości. Mimo że do najważniejszych kryteriów należy lekkość, zwykle konieczne jest zastosowanie ciężkich wkładek metalowych (stal, aluminium lub, w niektórych przypadkach, tytan), aby można było łączyć elementy wykonane z tworzyw sztucznych wzmocnionych włóknami węglowymi z innymi elementami mechanicznymi, co obniża nieco zalety włókien węglowych.
Rys. 1 przedstawia ramię robota do maszyny pakującej pracującej w przemyśle spożywczym. Przy całkowitej masie 300 g, ponad 80 g (27%) przypada na wkładki aluminiowe. Z tego powodu cel, jakim było zmniejszenie masy części (aby zredukować bezwładność), nie został w pełni osiągnięty. W nieprzyjaznych warunkach pracy, gdzie do czyszczenia stosowane są agresywne kwasy lub zasady (np. na automatycznych liniach pakowania produktów spożywczych), istnieje przy tej konfiguracji duże ryzyko wystąpienia korozji solnej lub galwanicznej.
Aluminium
Pomysł polegał na tym, aby zastąpić wkładkę wykonaną z aluminium (lub z innego, jeszcze cięższego metalu) wkładką wyprodukowaną z wysokosprawnego polimeru w celu zmniejszenia masy i ryzyka korozji oraz zapewnienia wysokiej sprawności mechanicznej wymaganej w przypadku omawianego zastosowania.
Wkładki metalowe z reguły przykleja się do części z materiału kompozytowego przy użyciu dwuskładnikowych klejów epoksydowych lub łączone bezpośrednio z ramą kompozytową, przy czym jako środka klejącego używa się żywicy matrycy polimerowej.
Niestety, jak wynika z literatury, siła sklejenia pomiędzy wkładką polimerową a częścią z materiału kompozytowego nie gwarantuje takiego samego poziomu przylegania, jak w przypadku przykładów przedstawionych w Tabeli 1. Wykres pokazuje, że wytrzymałość na ścinanie połączenia, które powstaje poprzez sklejenie różnych tworzyw termoplastycznych jest z reguły wyraźnie niższa od wartości granicznej 6 MPa, którą ogólnie traktuje się jako wielkość minimalną dla „strukturalnego“ złącza klejonego.
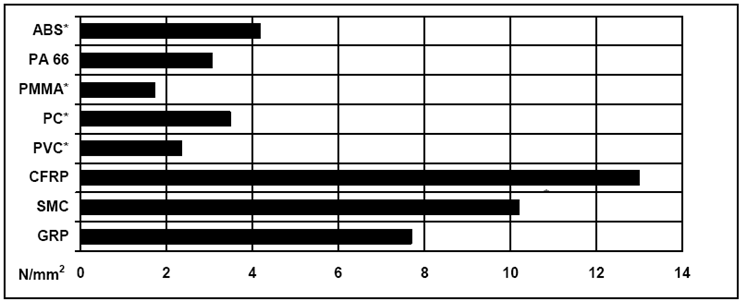
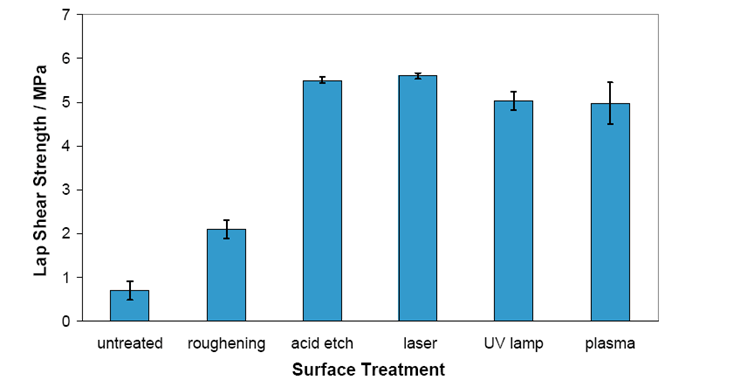
Również tutaj, przy zastępowaniu metalu tworzywem sztucznym, konieczne jest przeanalizowanie konstrukcji elementów i dostosowanie jej do nowego materiału. W związku z tym należy w pierwszej kolejności określić potencjalnie aspekty o decydującym znaczeniu, takie jak tolerancje, konstrukcje strukturalne i połączenia.
Przyleganie epoksydów do materiału PEEK jest zawsze znacznie mniejsze niż w przypadku metali. Tabela 2 przedstawia przykładowo złącze klejone w schemacie PEEK-PEEK z różnymi obróbkami powierzchni i w różnych warunkach. Widoczne są niskie parametry sklejonych powierzchni polimerowych.
W przypadku ramienia robota wykonanego z materiału kompozytowego pierwotna konstrukcja wkładki nie zapewniała bezpiecznego zamocowania komponentu do macierzy CRFP. Istniało ryzyko wystąpienia obrotów względnych pomiędzy wkładką a ramieniem.
Aby zrekompensować niskie parametry środka klejącego i uniknąć obrotów względnych pomiędzy elementami, zaprojektowano i wykonano połączenie mechaniczne pomiędzy wkładką z materiału TECAPEEK natural a kompozytowym elementem konstrukcyjnym wzmocnionym włóknem węglowym. Na przekroju przedstawionym na rys. 2 można zauważyć, że na wkładce z materiału TECAPEEK natural wykonano podcięcia, aby podczas laminowania mogła być bezpieczniej osadzona w elemencie konstrukcyjnym zawierającym włókna węglowe. Podcięcia we wkładce są całkowicie wypełnione laminowanym materiałem kompozytowym w celu wyeliminowania obrotów względnych obu elementów.
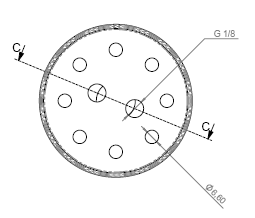
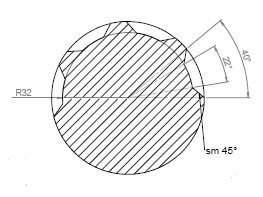

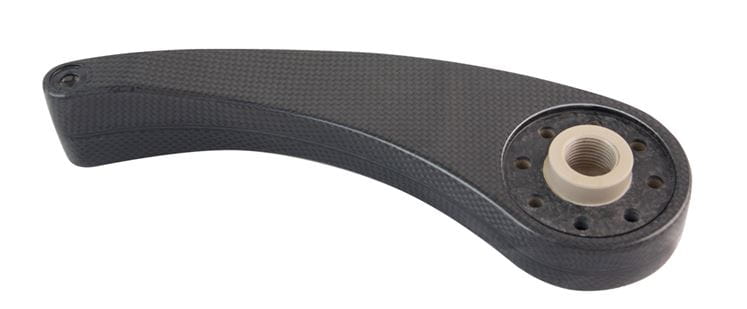
W ten sposób dla pierwotnego kompozytowego ramienia robota opracowano doskonałe, wymienialne rozwiązanie. Element konstrukcyjny ulepszono poprzez:
- zastosowanie wkładek wykonanych z wysokosprawnego tworzywa sztucznego (TECAPEEK natural), dzięki czemu – w porównaniu z wersją z wkładkami aluminiowymi – poprawiony został stosunek parametrów do masy zespołu konstrukcyjnego,
- uzupełnienie konstrukcji elementu o dodatkowe podcięcia, które podczas laminowania są bezpośrednio wypełniane matrycą z materiału kompozytowego, aby uniknąć stosowania substancji klejącej. Przy tym rozwiązaniu wyeliminowane zostają niepożądane obroty względne elementów.
- Zabezpieczenie przed korozją galwaniczną i chemiczną dzięki eliminacji części metalowych.
W przypadku tego rozwiązania całkowitą masę elementu zredukowano o prawie 15%, co z uwagi na mniejszy moment bezwładności powinno teoretycznie wpłynąć na zwiększenie prędkości i bezpieczeństwa pracy robota Delta.
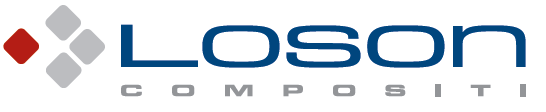