Bras de robot en composite
Dans cette étude de cas, Loson et Ensinger ont coopéré pour améliorer la performance d’un bras technique utilisé dans un robot Delta sur des lignes de conditionnement de denrées alimentaires. Les machines de ce type, rapides et précises, sont utilisées dans les usines pour la préhension et le conditionnement et permettent dans certains cas des fréquences de 300 préhensions par minute.
Les pièces en composite fibres de carbone - dans ce cas, des fibres de carbone sont tissées dans une matrice en époxy - sont conçues et réalisées afin de réduire le poids et l’inertie, tout en conservant les propriétés mécaniques typiques des alliages métalliques de haute qualité. La légèreté restant un des principaux objectifs, des inserts en métal, donc plus lourds (acier, aluminium ou, dans certains cas, titane) sont néanmoins nécessaires pour relier les pièces en composite fibres de carbone à d’autres composants mécaniques, réduisant l'avantage de la fibre de carbone.
La Fig. 1 montre un bras de robot pour une machine de conditionnement des aliments. D'un poids total d’environ 300 g, dont plus de 80 g (27 %) en aluminium, l’objectif de réduction de poids de la pièce (afin de réduire l’inertie) n'est que partiellement atteint. Dans des environnements agressifs, où des acides/bases sont utilisés pour le nettoyage (par exemple, sur les lignes de conditionnement des aliments), cette configuration est soumise à un risque élevé de corrosion par le sel ou à la corrosion galvanique.
L’aluminium
L’idée est de remplacer l'insert en aluminium (ou autre métal, donc encore plus lourd) par un polymère hautes performances afin de réduire le poids, le risque de corrosion et d'assurer les performances mécaniques exigées par l’application.
Les inserts en métal sont généralement collés aux pièces en composite par des colles époxy à deux composants ou encore directement incorporés dans le composite en utilisant la résine de la matrice polymère comme agent de collage.
Théoriquement, la force d’adhérence entre un insert en polymère et la partie composite ne peut malheureusemenet pas assurer le même niveau d’adhérence que ceux montrés dans le tableau n. 1. Ce graphique montre que la résistance au cisaillement d’un assemblage par collage de différents polymères thermoplastiques est en général en-dessous du seuil de 6 MPa, considéré par ailleurs comme le collage « structurel » minimum.
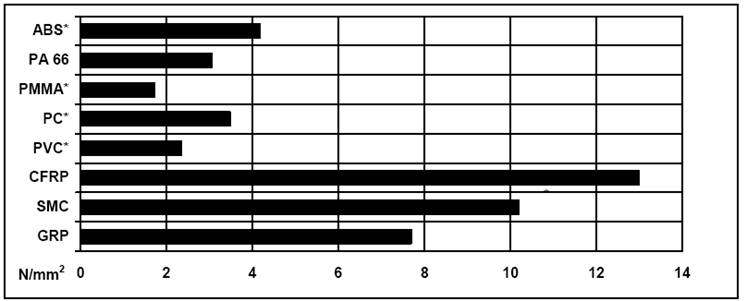
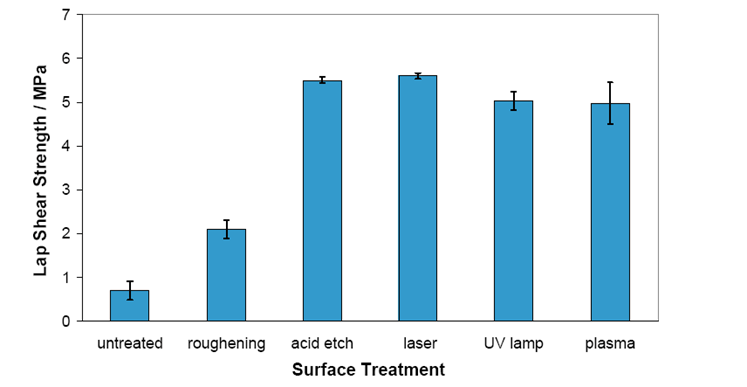
L'orsqu’on remplace un métal par du plastique, la conception des composants doit toujours être analysée et adaptée au nouveau matériau et ce, après avoir identifié et analysé les éventuels aspects critiques (comme la tolérance, la conception structurelle et les liens).
L’adhérence des pièces en époxy au PEEK est bien plus faible qu’au métal. Par exemple, le Tableau n. 2 montre le collage du PEEK au PEEK avec différents traitements de surface et dans diverses conditions, en soulignant les faibles performances des surfaces de polymères collés.
Dans le cas de bras de robot en composite, la conception de l’insert originel n’a pas assuré une adhérence suffisante du composant à la matrice CRFP, avec un risque de rotation relative entre l’insertion et le bras.
Pour surmonter la faible performance de la colle et empêcher la rotation relative des composants, nous avons conçu et réalisé un lien mécanique entre l’insertion en TECAPEEK natural et la pièce en composite fibres de carbone. La section transversale du dessin n. 1 montre des dégagements usinés dans l’insert en TECAPEEK natural pour permettre son intégration sans risque dans le composite à fibres de carbone pendant le procédé de lamination. Les dégagements dans les inserts sont entièrement comblés avec du matériau composite laminé afin d’empêcher toute rotation relative des deux composants.
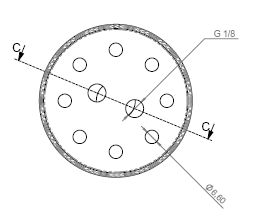
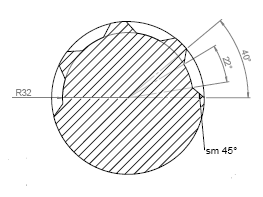
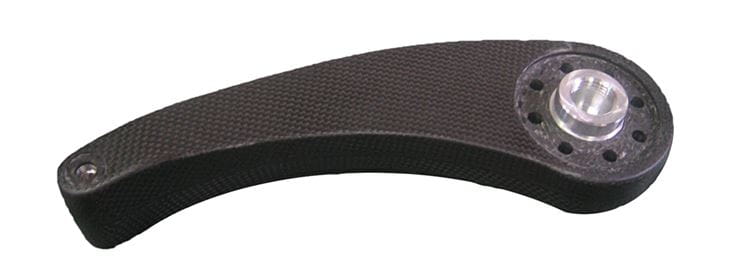
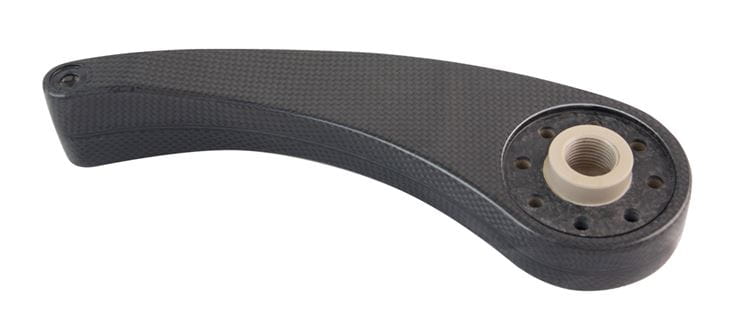
Une solution parfaitement interchangeable a été mise au point pour le bras de robot en composite original. Le composant a été amélioré par :
- L’utilisation d’inserts en plastique hautes performances usinés (TECAPEEK natural) qui augmente le rapport performance/poids de l’assemblage par rapport aux insertions en aluminium.
- La modernisation de la conception du composant, y compris les dégagements usinés directement remplis avec la matrice composite pendant le procédé de lamination pour éviter l’utilisation de la colle. Cette solution évite la rotation relative des composants.
- La protection contre la corrosion chimique et galvanique, validée grâce à l’absence des métaux.
Le poids total de la nouvelle pièce a été réduit de presque 15 %, permettant un fonctionnement minimisant les risques et plus rapide du robot Delta, grâce à un moment d’inertie plus faible.
