Braccio robotico composito
In questo studio applicativo, Loson ed Ensinger hanno collaborato per migliorare la prestazione di un braccio robotico usato in un Delta robot per le linee di confezionamento alimentare. Questi macchinari precisi e veloci vengono utilizzati nelle fabbriche per il prelievo e il confezionamento perché grazie alla loro rapidità è possibile, in alcuni casi, effettuare fino a 300 prelievi al minuto.
I particolari compositi in fibra di carbonio (in questo caso tessuto in fibra di carbonio su matrice epossidica) vengono progettati e prodotti per ridurre peso e inerzia, conservando le elevate proprietà meccaniche tipiche delle leghe metalliche di alta qualità. Nonostante la leggerezza sia uno degli obiettivi principali, gli inserti in metallo pesante (acciaio, alluminio o, in alcuni casi, titanio) sono solitamente necessari per collegare parti composite in fibra di carbonio con altri componenti meccanici, così che il beneficio della fibra di carbonio risulta parzialmente ridotto.
L'immagine qui sopra mostra un braccio robotico realizzato per un macchinario per l’industria del confezionamento alimentare: del peso totale di 300 gr, più di 80 g (27%) sono rappresentati dai inserti in alluminio, pertanto lo sforzo di ridurre il peso del componente (per ridurre l’inerzia) risulta in parte compromesso. Inoltre, negli ambienti di lavoro più difficili, in cui vengono utilizzati detergenti acidi/basici come le linee di confezionamento alimentare, questa configurazione è soggetta ad un elevato rischio di corrosione salina o elettrolitica.
Alluminio
L’idea è quella di sostituire un inserto in alluminio (o altro metallo, e quindi anche più pesante) utilizzando un polimero ad alte prestazioni per ridurre il peso, ridurre il rischio di corrosione e, allo stesso tempo, garantire le elevate prestazioni meccaniche richieste dall’applicazione.
Gli inserti in metallo sono solitamente collegati alle parti composite utilizzando colle epossidiche bicomponenti, oppure sono direttamente incorporate nella struttura del composito utilizzando la resina della matrice polimerica come agente legante.
Sfortunatamente, considerando i dati, la resistenza del legame tra un inserto polimerico e la parte composita non può garantire lo stesso livello di adesione, come visto, ad esempio, nella Tavola n. 1. Questo grafico mostra che la resistenza al taglio di una connessione mediante incollaggio di due differenti polimeri termoplastici è solitamente ben al di sotto della soglia di 6 MPa, generalmente considerato il livello minimo per l’incollaggio “strutturale”.
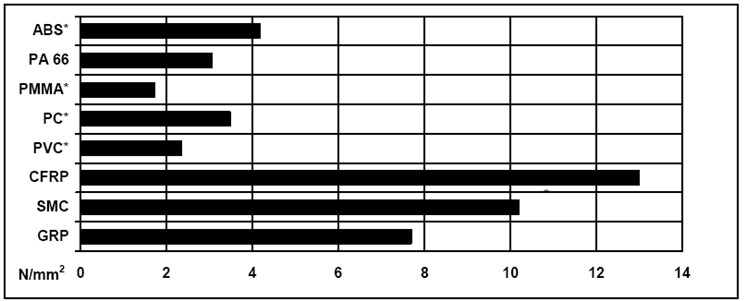
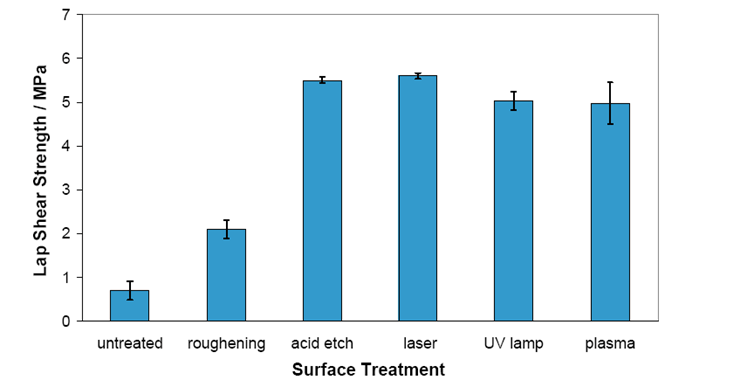
Come sempre, quando si sostituisce un metallo con un materiale plastico, il design del componente deve essere analizzato e adattato al nuovo materiale dopo aver individuato eventuali aspetti critici quali le tolleranze, il design strutturale e le connessioni.
L’adesione degli epossidici al PEEK è sempre molto più bassa di quella al metallo. Ad esempio, la Tavola n. 2 mette in evidenza il PEEK su PEEK incollato con diversi trattamenti superficiali e in varie condizioni e sottolinea le basse prestazioni delle superfici polimeriche incollate.
Nel caso di questo braccio robotico composito, il progetto originale dell’inserto non garantiva la sicura adesione del componente alla matrice CFRP, con il rischio di rotazione relativa tra l’inserto e il braccio.
Per superare la bassa prestazione della colla ed evitare la rotazione relativa dei componenti, è stata progettata e prodotta una connessione meccanica tra l’inserto in TECAPEEK natural e la parte composita in fibra di carbonio. Come mostra la sezione trasversale del disegno n. 2, vengono realizzati dei sottosquadri nell’inserto in TECAPEEK natural così che possa essere incorporato in modo sicuro nella parte composita in fibra di carbonio, durante il processo di laminazione. I sottosquadri dell’inserto vengono completamente riempiti con il materiale composito laminato per escludere ogni rotazione relativa dei due componenti.
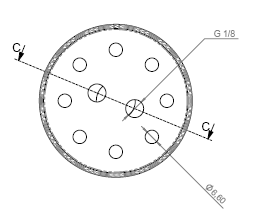

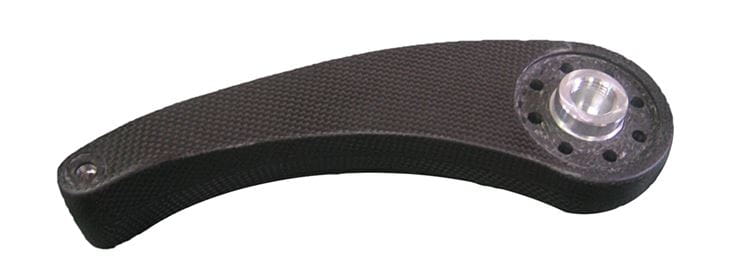
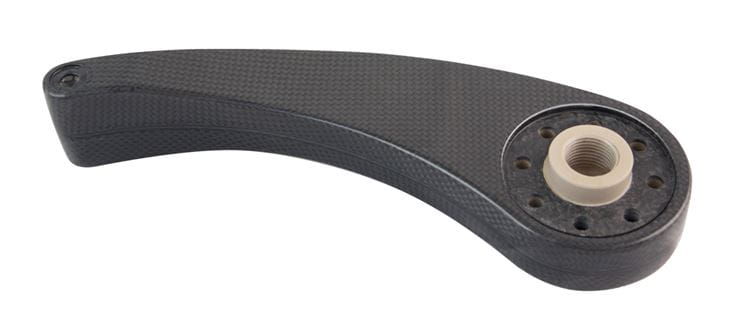
In questo studio è stata progettata una soluzione perfettamente intercambiabile per il braccio robotico composito originale. Il componente è stato migliorato come segue:
- L’uso di inserti ottenuti da materiale plastico ad alte prestazioni (TECAPEEK natural), che migliora il rapporto prestazione/peso dell’assemblato rispetto agli inserti in alluminio.
- La progettazione migliorata del componente realizzando sottoquadri, riempiti direttamente con la matrice composita durante la procedura di laminazione per evitare l’uso di colla. Questa soluzione evita la rotazione relativa indesiderata dei componenti.
- Protezione dalla corrosione elettrolitica e chimica, grazie all’assenza di metalli.
Grazie a questa soluzione il peso totale della parte è stato ulteriormente ridotto di quasi il 15%, consentendo, in teoria, un’operatività più rapida e sicura del Delta robot grazie al ridotto momento d’inerzia.
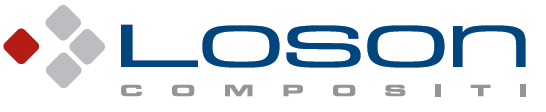