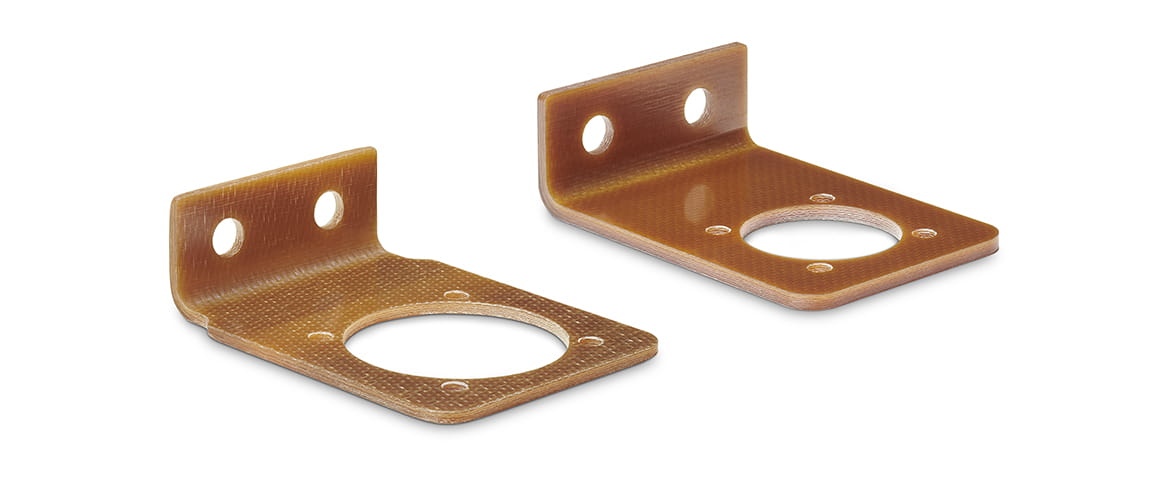
Fästen för elanslutningar
Lätta konstruktioner i flygplansinteriörer: kompositbaserade serietillverkade komponenter
Lätta och höghållfasta material har blivit oumbärliga för avancerade applikationer inom flygindustrin. I passagerarflygplan räknas varje kilo, varför metaller i allt högre grad ersätts med plastbaserade lösningar, även inom inredningsdesign. I synnerhet termoplastiska kompositer erbjuder företag som planerar flygplan betydande viktminskning utan att de behöver kompromissa när det gäller mekaniska egenskaper. Ett projekt av företagen Bucher Leichtbau och Ensinger visar att övergången till fiberförstärkta kompositer kan ge ytterligare tekniska fördelar.
Bucher Leichtbau AG, med huvudkontor i Fällanden (Schweiz), är specialist på flyginredning och fordonsutrustning. Bland annat utvecklar och producerar företagsgruppen pentryn och skåp för passagerarflygplan. En hel modul av denna typ kan rymma en belastning som motsvarar åtta gånger sin egen vikt och måste kunna motstå accelerationer som är minst nio gånger tyngdacceleration. Här görs en åtskillnad mellan flygbelastningar (normala flygförhållanden som start, landning, turbulens) och nödlandningsbelastningar (kontrollerad nödlandning eller avbruten start). Den erforderliga minimilivslängden för producerade moduler är till exempel 25 år för Airbus och Boeing.
initiala situationen
Av säkerhetsskäl måste alla metallfästen för elektriska plug-in-anslutningar i kommersiell luftfart jordas. Med elektriskt ledande stödkonstruktioner i Buchers aluminium pentry är en befintlig fästskruv utrustad med nödvändiga korrosionsskyddsåtgärder ofta tillräcklig. Om emellertid metallkopplingsfästena är placerade på icke-ledande strukturer i köket, krävs en extra kabel för den elektriska jordning. Denna jordningskabel måste säkras med jämna mellanrum vilket skapar krav på ytterligare gängor, distansbultar, kabelklämmor och skruvar.
Förutom materialåtgång för kabeldragningen uppstår höga kostnader för planering och installation: I konstruktionsarbetet ingår att göra en post i det schematiska kretsschemat; dessutom måste en motståndsmätning definieras i testplanen för varje jordkabel. Detta måste också införlivas i relevanta underhållsriktlinjer och driftsinstruktioner samt i auktoriseringsdokumenten. Under produktionen måste kontaktmotståndet registreras och en korrosionsskyddsbeläggning appliceras vid varje jordanslutning.
Termoplastisk komposit ersätter behovet av jordning
Arbetet och kostnaderna för en jordanslutning kan elimineras helt om kontaktfästena som tidigare gjorts av metall ersätts av en icke-ledande variant. På grund av drifttemperaturen och brandsäkerhetskraven är det dock inte möjligt att använda en billig standardplast.
Det eftertraktade tekniska alternativet behövde kunna ersätta ett stort antal befintliga aluminiumdelar en-mot-en för att minimera arbetet och kostnaderna för att byta när de infördes. För att detta krav ska kunna tillgodoses krävs ett styvt, höghållfast material.
På grund av de relativt små mängderna av olika anslutningsfästen var en lösning med höga verktygskostnader inte ett alternativ. Inledande försök med lokalt ombyggda delar tillverkade av fiberförstärkt termoplastiska skivor visade inte tillfredsställande resultat i de ombyggda zonerna.
I arbetet med Ensingers Composite-division hittades snabbt en lämplig lösning på basis av termoplastfiberarmerad komposit. En prepreg godkänd för flygindustrin med glasfiber och en PEI-matris (polyeterimid) valdes för materialet. Efter en kort optimeringsfas var det möjligt att tillverka de första serieproducerade delarna. På grund av den specialiserade bearbetningstekniken är två av Ensingers anläggningar involverade i produktionen av anslutningsfästen:
På Otelfingen-anläggningen producerar Ensingers kompositexperter halvfärdiga delar i vinkelform från PEI-prepregs. Till skillnad från jämförbara komponenter, skärs dessa ämnen inte i storlek från ett tjockt laminat och värmeformas utan pressas med hjälp av enskilda prepreg-lager i ett verktyg till den definierade formen. Bland annat erbjuder denna process fördelen att den reducerar backback-effekten. CNC-bearbetningen av fiberkompositdelarna sker på Ensinger GmbH i Cham i Bayern.
Cham-bearbetningsavdelningen, som specialiserat sig på produktion av precisionsdelar av termoplastiska högpresterande plast och kompositmaterial, ingår i Ensingers internationella bearbetningsgrupp.
För de flesta fästen finns det flera versioner med olika dimensioner. Tack vare den flexibla processen är det också möjligt att producera högkvalitativa specialkonstruktioner med konturer eller borrade hål och med korta ledtider.
Enklare, mer kostnadseffektivt och lättare
INNAN CNC-BEARBETNING
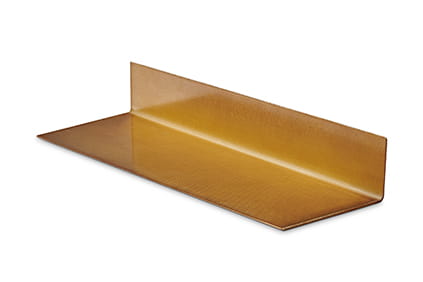
Ett ämne för ett fäste för en plug-in-anslutning är tillverkad av en fiberkomposit, godkänd för flygindustrin med glasfiber som är inbäddad i en PEI-matris.
Kontaktfästena finns i versioner med olika dimensioner. Tack vare de kontinuerliga, rätade fibrerna har det termoplastiska kompositmaterialet betydligt högre hållfasthet och styvhet än kort fiberförstärkt plast.
PREFORM TEKNIK
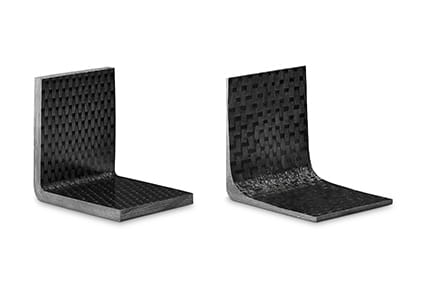
Tack vare Ensingers förformsteknik är skillnader i väggtjocklekar också möjliga när man producerar vinklar. Så som en gaffelformad gren kan hörnsektionen under höga spänningar förstärkas, medan i sektionerna som inte är under höga spänningar (t.ex. på armarna) kan material sparas. Tillverkningstekniken kallas ”near net shape”.
Beroende på komponentgeometrin är betydande material- och viktbesparingar möjliga med denna teknik - samtidigt som man bibehåller jämförbar styrka och styvhet.