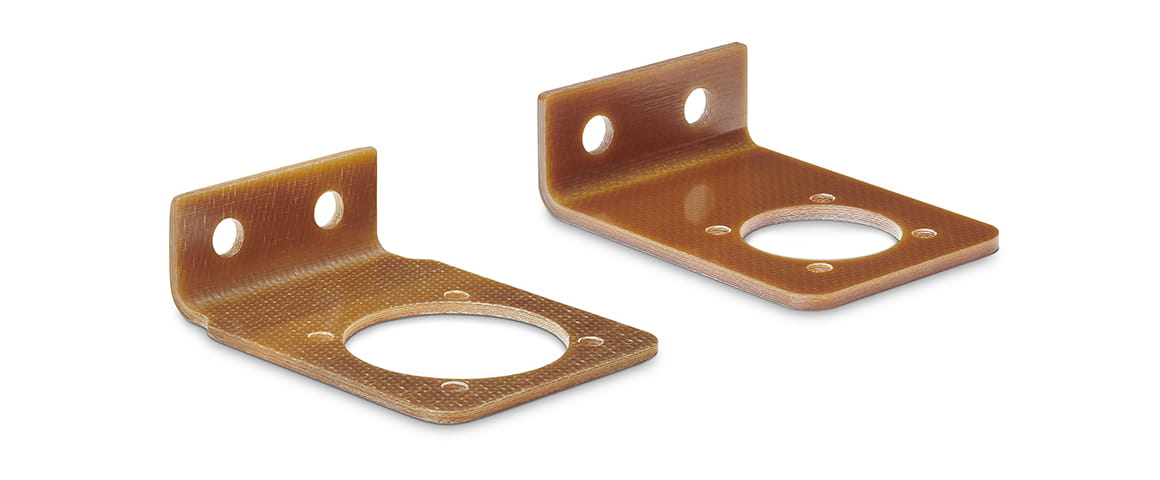
Beslag til konnektorer til elektriske stik
Letvægtskonstruktioner i flyinteriører: Kompositbaserede serieproducerede komponenter
Letvægt og høj-styrke materialer er blevet uundværlige i high-end anvendelser i luft- og rumfartsindustrien. I passagerfly tæller alle kilo, hvilket er hvorfor metaller mere og mere erstattes af plastbaserede løsninger, også i design af interiør. Særligt termoplast kompositter giver virksomhederne en signifikant mulighed for at finde løsninger, der er vægtreducerende og samtidigt ikke kompromitterer de mekaniske egenskaber. Et projekt af virksomhederne Bucher Leichtbau og Ensinger viser, at ved at skifte til fiber-forstærkede kompositter, kan der opnås yderligere tekniske fordele.
Bucher Leichtbau AG, med hovedkvarter i Fällanden (Schweiz) er specialist i flyinteriør og udstyr til bilindustrien. Blandt andet, udvikler og producerer fly divisionen i virksomhedsgruppen kabinetter og pantries til passagerfly. Et fuldt modul i denne type skal imødekomme en belastning svarende til otte gange sin egen vægt og skal være i stand til at modstå accelerationer, som er mindst ni gange så stor som tyngdekraftsaccelerationen. Her er der en forskel på flybelastninger (normale betingelser for flyvninger, så som take-off, landing og turbulens) og belastinger i nødsituationer (en kontrolleret nødlanding eller afbrudt start). Den krævede minimum levetid for de producerede moduler er for eksempel 25 år for Airbus og Boeing.
Udgangspunktet
Af sikkerhedsgrunde, skal alle metalbeslag til elektriske stik konnektorer i den kommercielle flyindustri have forbindelse til jord. Med elektrisk ledende understøttende strukturer i Bucher aluminium pantries, er en eksisterende fastgørelsesskrue, udstyret med den nødvendige korrosionsbeeskyttelse ofte tilstrækkelig. I nogle situationer, hvis metalkonnektor beslagene er placeret på ikke ledende strukturer i pantriet, er det nødvendigt med et ekstra kabel, for at sikre jordforbindelse. Dette kabel til jordforbindelse skal sikres med jævnlige intervaller, hvilket indebærer et krav til yerligere fastgøringstråde, afstandsbolte, kabelklemmer og skruer.
I tillæg til materialekrav til kabelføring, kommer der høje omkostninger oveni til planlægning og installering: Designarbejdet inkluderer at tilføje en post til det skematiske kredsløbsdiagram; oveni skal der defineres en modstandsmåling i testplanen for hvert enkelt kabel med jordforbindelse. Dette skal også indarbejdes i de relevante retningslinjer for vedligeholdelse og anvendelse, såvel som i autorisationsdokumenterne. Under produktion skal kontaktmodstanden registreres og en korrosionsbeskyttelse skal påføres alle jordforbindelser.
erstatning med termoplast kompositter fjerner behovet for jordforbindelse
Arbejdet og omkostningerne forbundet med en jordforbindelse kan elimineres fuldstændigt, hvis konnektor beslagene tidligere produceret i metal, erstattes med en ikke-ledende variant. På grund af arbejdstemperaturen og krav til brandsikkerhed, er det ikke muligt at anvende en standard plast.
De efterspurgte tekniske alternativer skulle kunne erstatte et stort antal aluminiumdele en-til-en, for at kunne minimere arbejdet og omkostningerne ved at skifte. For at dette krav kunne imødekommes, var det nødvendigt med et stift materiale, der også havde høj styrke.
På grund af de relativt små mængder af de forskellige konnektor beslag, var det ikke muligt med en løsning med store værktøjsomkostninger. Indledende forsøg med lokalt ombyggede dele i fiberforstærket, termoplast plademateriale viste ikke tilfredsstillende resultater i de ombyggede områder.
I samarbejdet med Ensinger’s Kompositdivision blev der fundet en anvendelig løsning på basis af termoplast fiberforstærket komposit. En prepreg godkendt til flyindustrien med glasfiber og en PEI matrix (polyetherimide) blev valgt. Efter en kort optimeringsfase, var det muligt at producere de første serieproducerede dele. På grund af de specialiserede bearbejdningsteknikker, er to af Ensingers lokationer involverede i produktionen af konnektorbeslagene.
På vores Otelfingen site, producerer Ensinger's kompositeksperter halvfabrikata vinkelformede dele af PEI prepregs. I modsætning til sammenlignelige komponenter, bliver disse dele ikke skåret på mål fra et laminat og termoformet, men fremstilles ved at presse de individuelle prepreg lag til den definerede form i et værktøj. Blandt andet giver denne proces fordelen i en reduceret effekt i, at materialet springer tilbage til sin udgangsform CNC bearbejdningen af delene i fiberkomposit finder sted hos Ensinger GmbH i Cham i Bavaria.
Chams bearbejdningsafdeling, som er specialiseret i produktionen af præcisionsdele i high-performance termoplast og komposit materialer, en del af Ensinger’s internationale gruppe af bearbejdere. Fra de firkantede emner færdigbearbejder Otelfingen og Ensinger Cham med præcision konnektor beslagene til de endelige specifikationer for produktet.
For de fleste fastgørelsesbeslag er der flere versioner med forskellige dimensioner. Takket være den fleksible propces, er det også muligt at producere specielle designs i høj kvalitet, specielle design med konturer eller borede huller og med kort leveringstid.
Mere enkelt, omkostningseffektivt og lettere
Fremstillingsomkostningerne for de nye plastbeslag er signifikant højere end end for den tidligere version i aluminium. Men besparelserne på bearbejdning og produktion af kabinetterne betyder at den nye løsning stadig er mere enkel og vigtigere mere omkostningseffektiv samlet set. Løsningen er lettere takket være kompositkomponenterne, hvilket giver en fordel for flyene på længere sigt, da hvert enkelt kilo ekstra vægt, som kan spares under flyvning, betyder økonomiske besparelser.
Før CNC bearbejdning
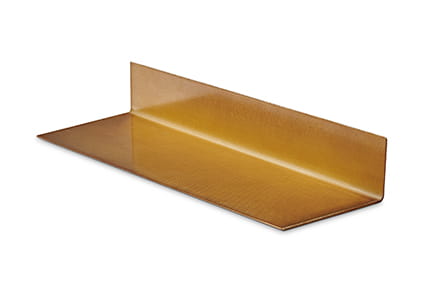
Et ark til et beslag til konnektorer konstrueres af et fiberkomposit pre-preg, godkendt til luftfart industrien med glasfiber, som er indlejret i en PEI matrice.
Konnektorbeslagene findes i versioner med forskellige dimensioner. Takket være de fortløbende rette fibre, har termoplast komposit materialet signifikant højere styrke and stivhed end kortfibrede forstærkede plasttyper.
PREFORM TEknologi
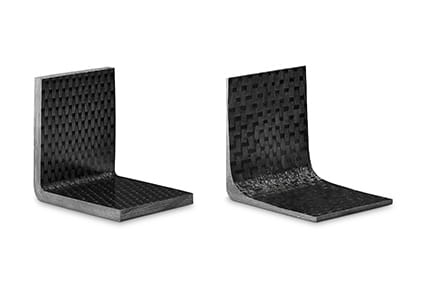
Takket være Ensinger's preform teknologi, er forskelle i vægtykkelser også mulige, når der produceres hjørner. Så hjørnesektionen, der er under høj stresspåvirkning kan forstærkes, mens materiale kan spares for de sektioner, som ikke er påvirket af høj stress. Fremstillingsteknikken kaldes en "near net shape’ proces.
Afhængigt af komponentens geometri, er det muligt at gøre signifikante besparelser med denne teknologi - samtidigt med at der bibeholdes styrke og stivhed.