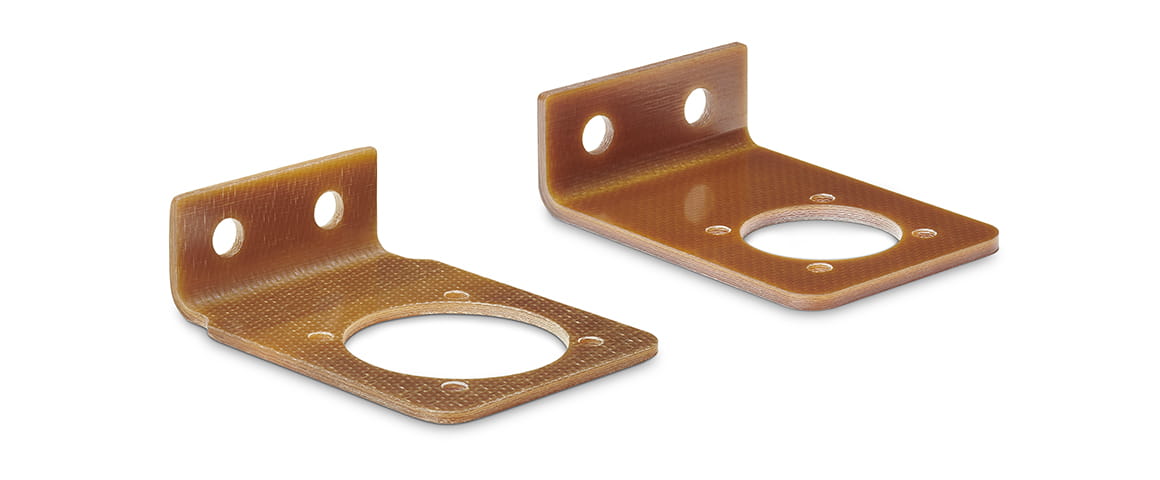
Supporti per connettori elettrici
Costruzioni ultraleggere per interni di aerei: componenti in composito prodotti in serie
Materiali leggeri e ad elevata resistenza meccanica sono diventati indispensabili per le applicazioni di fascia alta nell'industria aeronautica. Negli aerei passeggeri è importante ogni singolo chilogrammo, per cui i metalli vengono sempre più spesso sostituiti con soluzioni in materiale plastico, anche per l'arredamento degli interni. I compositi termoplastici, in particolare, offrono alle aziende che allestiscono gli aerei significativi risparmi di peso, senza compromessi in termini di proprietà meccaniche. Un progetto sviluppato dalle aziende Bucher Leichtbau ed Ensinger mostra come il cambio verso compositi fibrorinforzati può dare anche ulteriori vantaggi tecnici.
Bucher Leichtbau AG, con sede principale a Fällanden (Svizzera), è specializzata in interni di aerei ed equipaggiamenti per auto. Tra le altre cose, la divisione aviazione del gruppo progetta e produce cambuse e armadietti per aerei passeggeri. Un modulo completo di questo tipo può ospitare un carico corrispondente a otto volte il suo peso e deve essere in grado di resistere ad accelerazioni fino a nove volte quella gravitazionale. Qui si fa distinzione tra carichi di volo (condizioni di volo normali come decollo, atterraggio, turbolenza) e carichi di emergenza (atterraggio di emergenza controllato o decollo interrotto). La vita operativa minima richiesta per i moduli prodotti è, ad esempio, di 25 anni per Airbus e Boeing.
situazione iniziale
Per motivi di sicurezza, nell'aviazione commerciale tutti i supporti metallici per connettori elettrici devono essere messi a terra. Nel caso delle cambuse in alluminio Bucher, con strutture portanti elettroconduttive, spesso è sufficiente una semplice vite di fissaggio dotata delle necessarie misure di protezione contro la corrosione. Se invece i supporti metallici dei connettori delle cambuse sono posizionati su strutture non conduttive, è necessario un cavo aggiuntivo per la messa a terra. Questo cavo deve essere fissato a intervalli regolari, il che comporta l'utilizzo di ulteriori filetti di fissaggio, bulloni distanziali, morsetti per cavi e viti.
Oltre all'impiego di materiale aggiuntivo per la posa dei cavi, questo comporta elevati costi di progettazione e installazione: il lavoro di progettazione comprende l'inserimento di questi elementi nello schema del circuito elettrico; inoltre, nel piano di collaudo bisogna definire una misura della resistenza elettrica per ciascun cavo di messa a terra. Questi componenti vanno anche incorporati nelle relative linee guida di manutenzione e nelle istruzioni operative, così come nei documenti di autorizzazione. Durante la produzione, occorre inoltre registrare la resistenza di contatto ed applicare un rivestimento anticorrosione su ogni messa a terra.
i compositi termoplastici evitano la necessità di messa a terra
È possibile eliminare completamente il lavoro e i costi legati alla messa a terra se i supporti metallici dei connettori vengono sostituiti da una variante non conduttiva. A causa della temperatura d'esercizio e dei requisiti di sicurezza antincendio, non è possibile utilizzare una plastica standard a basso costo.
Un'eventuale alternativa tecnica doveva essere in grado di sostituire singolarmente un gran numero di parti esistenti in lamiera di alluminio, in modo da ridurre al minimo il lavoro e i costi di sostituzione al momento dell'introduzione. Per soddisfare questa richiesta era dunque necessario un materiale isolante, rigido e ad alta resistenza meccanica.
Viste le quantità relativamente piccole e la grande varietà di supporti dei connettori, qualsiasi soluzione con alti costi di attrezzatura era da scartare. Le prove iniziali in tradizionale materiale termoplastico rinforzato con fibre, con parti rimodellate sul posto, non hanno mostrato risultati soddisfacenti nelle zone deformate plasticamente.
Lavorando con la divisione Compositi di Ensinger, è stata trovata rapidamente una soluzione adatta utilizzando i compositi termoplastici rinforzati con tessuto. Il materiale scelto è stato un prepreg approvato per l'industria aeronautica, con fibra di vetro e matrice in PEI (polieterimmide). Dopo una breve fase di ottimizzazione, è stato possibile produrre i primi pezzi in serie. A causa delle tecniche di trasformazione specializzate, nella produzione dei supporti dei connettori sono coinvolti due diversi siti Ensinger:
Nel sito di Otelfingen, gli esperti di compositi di Ensinger producono parti semi-finite di forma angolare a partire dai prepreg in PEI. A differenza di componenti simili, questi grezzi non vengono tagliati su misura da una lastra e termoformati o piegati, ma, utilizzando singoli strati di prepreg, vengono pressati in uno stampo nella forma definita. Tra le altre cose, questo processo ha anche il vantaggio di ridurre l'effetto di ritorno elastico. La lavorazione CNC finale delle parti in composito viene fatta presso Ensinger GmbH a Cham, in Baviera.
l reparto di lavorazioni meccaniche di Cham, specializzato nella produzione di pezzi di precisione in termoplastici ad alte prestazioni e materiali compositi, è membro del gruppo internazionale di lavorazione Ensinger. I supporti di fissaggio dei connettori vengono lavorati secondo le specifiche finali del prodotto a partire dagli sbozzati angolari prodotti a Otelfingen.
Per la maggior parte dei supporti di fissaggio ci sono diverse versioni con diverse dimensioni. Grazie al processo produttivo estremamente flessibile, è possibile ottenere con tempi di consegna brevi anche design personalizzati di alta qualità che contengono contorni speciali o fori.
Più semplici, più convenienti e più leggeri
I costi di produzione dei nuovi supporti in plastica sono significativamente più alti rispetto alla versione precedente in alluminio. Tuttavia, i risparmi in termini di progettazione e produzione degli armadietti fanno sì che la nuova soluzione sia notevolmente più semplice e, soprattutto, più conveniente nel complesso. Dato che, grazie all'uso di componenti compositi, le cambuse sono più leggere, le compagnie aeree ne traggono vantaggi a lungo termine, perché ogni chilogrammo di peso aggiuntivo che non deve essere portato in volo fa risparmiare denaro.
Prima della lavorazione CNC
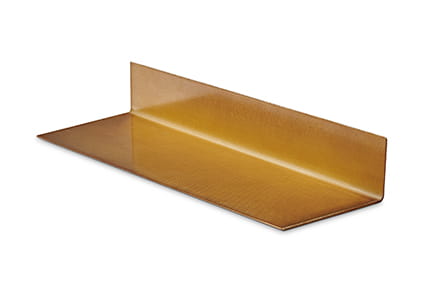
Il grezzo della staffa per connettori viene costruito da un pre-preg composito in fibra approvato per l'industria aeronautica, con fibre di vetro impregnate in matrice di PEI.
I supporti per connettori hanno diverse versioni e dimensioni. Grazie alle fibre continue e orientate, il composito termoplastico ha una resistenza meccanica e una rigidezza notevolmente superiore rispetto alle plastiche rinforzate con fibra corta.
Tecnologia di preformatura
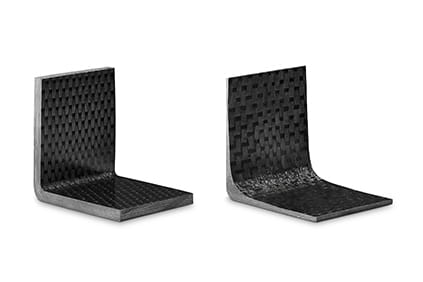
Grazie alla tecnologia di preformatura Ensinger è possibile produrre anche angolari a spessore variabile. In maniera simile a un ramo che si biforca, è possibile rinforzare la sezione angolare dove è sottoposta a maggiore carico, mentre nelle sezioni meno sollecitate (es. quelle terminali) si può risparmiare materiale. La tecnologia viene chiamata processo ‘near net shape’.
Con questa tecnologia, a seconda della geometria del componente, è possibile risparmiare in modo significativo materiale e peso, mantenendo resistenza meccanica e rigidità comparabili.