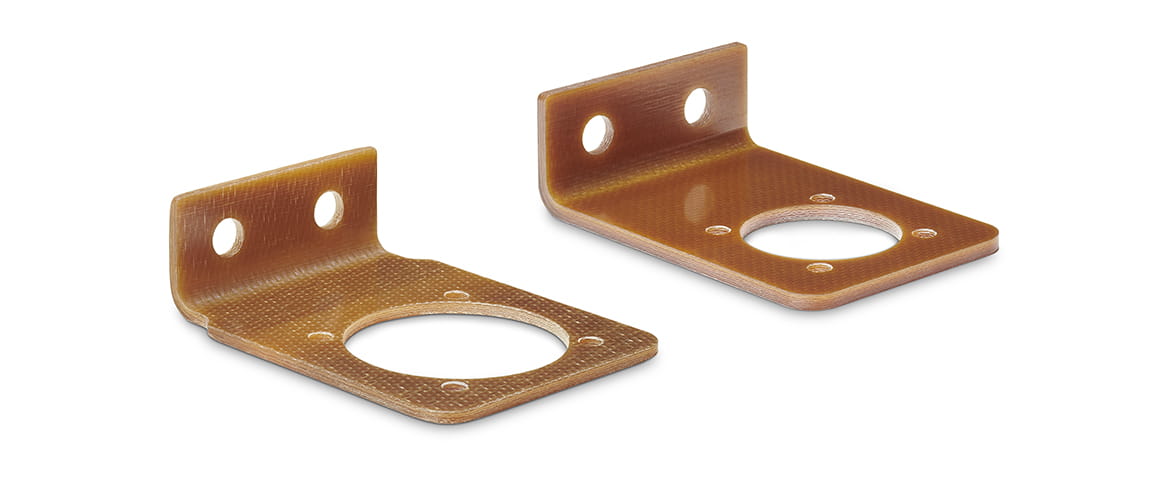
Fixations pour connexions électriques enfichables
Intérieurs d'avions de construction légère : composants fabriqués en série à base de composites
Les matériaux légers et à haute résistance sont devenus indispensables pour les applications haut de gamme dans l'industrie aéronautique. Dans les avions de passagers, chaque kilogramme compte, c'est pourquoi les métaux sont de plus en plus remplacés par des solutions à base de plastique, également dans la décoration intérieure. Les composites thermoplastiques, en particulier, offrent aux entreprises d'équipement d'avions une réduction de poids significative sans les obliger à faire des compromis en termes de propriétés mécaniques. Un projet des sociétés Bucher Leichtbau et Ensinger montre que le passage aux composites renforcés de fibres peut offrir des avantages techniques supplémentaires.
Bucher Leichtbau AG, dont le siège est à Fällanden (Suisse), est un spécialiste des intérieurs d'avions et des équipements automobiles. Entre autres choses, la division aviation du groupe d'entreprises développe et produit des galleys et des armoires pour les avions de passagers. Un module complet de ce type peut accueillir une charge correspondant à huit fois son propre poids et doit pouvoir supporter des accélérations au moins neuf fois supérieures à l'accélération gravitationnelle. Ici, une distinction est faite entre les charges de vol (conditions de vol normales telles que décollage, atterrissage, turbulence) et les charges d'atterrissage d'urgence (atterrissage d'urgence contrôlé ou décollage interrompu). La durée de vie minimale requise des modules produits, est par exemple de 25 ans pour Airbus et Boeing.
situation INITIALE
Pour des raisons de sécurité, tous les supports métalliques pour les connexions électriques enfichables dans l'aviation commerciale doivent être mis à la terre. Avec des structures de support électriquement conductrices dans les cuisines en aluminium Bucher, une vis de fixation existante équipée des mesures de protection contre la corrosion nécessaires est souvent suffisante. Si toutefois les supports de connecteurs métalliques sont positionnés sur des structures non conductrices dans les cuisines, un câble supplémentaire est nécessaire pour la mise à la terre électrique. Ce câble de mise à la terre doit être fixé à intervalles réguliers, ce qui nécessite des filetages de fixation supplémentaires, des boulons d'écartement, des serre-câbles et des vis.
En plus de l'apport de matériel pour le cheminement des câbles, des coûts élevés se posent pour la planification et l'installation : le travail de conception comprend la création d'une entrée dans le schéma de circuit ; de plus, une mesure de résistance doit être définie dans le plan de test pour chaque câble de mise à la terre. Cela doit également être intégré dans les directives d'entretien et les instructions d'exploitation pertinentes, ainsi que dans les documents d'autorisation. Pendant la production, la résistance de contact doit être enregistrée et un revêtement de protection contre la corrosion doit être appliqué à chaque connexion à la terre.
Le substitut de composite thermoplastique élimine le besoin de mise à la terre
Le travail et les coûts impliqués dans une connexion à la terre peuvent être complètement éliminés si les supports de connecteur précédemment réalisés en métal sont remplacés par une variante non conductrice. Cependant, en raison des exigences de température de fonctionnement et de sécurité incendie, il n'est pas possible d'utiliser un plastique standard à faible coût.
L'alternative technique recherchée devait être capable de remplacer un à un un grand nombre de pièces en tôle d'aluminium existantes afin de minimiser le travail et les coûts de changement lors de leur introduction. Pour que cette demande soit satisfaite, un matériau rigide et à haute résistance est requis.
En raison des quantités relativement faibles des différents supports de connecteur, une solution avec des coûts d'outillage élevés n'était pas une option. Les premiers essais avec des pièces localement remodelées en matériau en feuille thermoplastique renforcé de fibres n'ont pas montré de résultats satisfaisants dans les zones remodelées.
En collaboration avec la division Composite d'Ensinger, une solution adaptée à base de composite thermoplastique renforcé de fibres a été rapidement trouvée. Un préimprégné approuvé pour l'industrie aéronautique avec de la fibre de verre et une matrice PEI (polyétherimide) a été choisi pour le matériau. Après une brève phase d'optimisation, il a été possible de fabriquer les premières pièces produites en série. En raison des techniques de traitement spécialisées, deux des sites d'Ensinger sont impliqués dans la production des supports de connecteurs :
Sur le site d'Otelfingen, les experts composites d'Ensinger produisent des pièces semi-finies de forme angulaire à partir des préimprégnés PEI. Contrairement à des composants comparables, ces flans ne sont pas découpés sur mesure à partir d'un stratifié épais et thermoformés mais, à l'aide de couches préimprégnées individuelles, pressés dans un outil dans la forme définie. Ce procédé offre entre autres l'avantage de réduire l'effet de retour élastique. Le traitement CNC des pièces en fibre composite a lieu chez Ensinger GmbH à Cham en Bavière.
Le département d'usinage Cham, spécialisé dans la production de pièces de précision à partir de plastiques thermoplastiques hautes performances et de matériaux composites, est membre du groupe d'usinage international d'Ensinger. À partir des ébauches angulaires produites à Otelfingen, Ensinger à Cham usine les supports de connecteurs jusqu'aux spécifications du produit final.
Pour la plupart des supports de fixation, il existe plusieurs versions avec des dimensions différentes. Grâce au processus flexible, il est également possible de produire des conceptions spéciales de haute qualité avec des contours ou des trous percés et avec des délais de livraison courts.
Plus simple, plus économique et plus léger
AVANT LE TRAITEMENT CNC
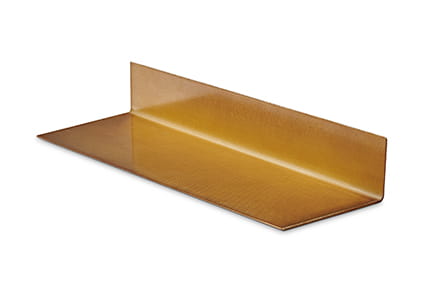
Un cache pour un support pour une connexion enfichable est construit à partir d'un pré-imprégné composite de fibres, approuvé pour l'industrie aéronautique avec de la fibre de verre qui est intégrée dans une matrice PEI.
Les supports de connecteur sont disponibles dans des versions avec différentes dimensions. Grâce aux fibres continues et redressées, le matériau composite thermoplastique présente une résistance et une rigidité nettement supérieures à celles des plastiques courts renforcés de fibres.
TECHNOLOGIE DES PRÉFORMES
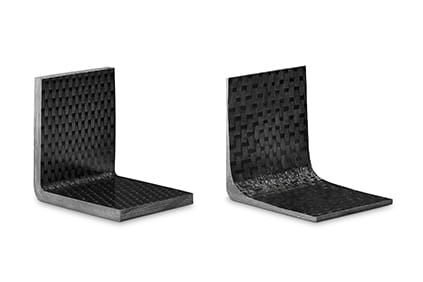
Grâce à la technologie des préformes d'Ensinger, des différences d'épaisseur de paroi sont également possibles lors de la production d'angles. Si semblable à une branche fourchue, la section d'angle sous fortes contraintes peut être renforcée, tandis que dans les sections qui ne sont pas sous fortes contraintes (par exemple sur les bras), la matière peut être économisée. La technique de fabrication est appelée processus de « forme quasi nette ».
Selon la géométrie des composants, des économies significatives de matière et de poids sont possibles avec cette technologie, tout en conservant une résistance et une rigidité comparables.