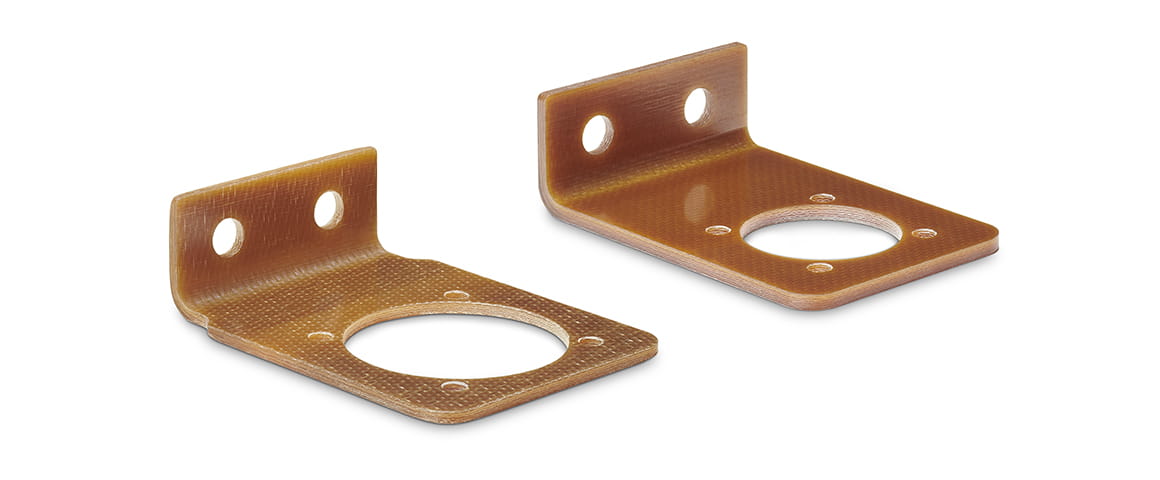
Tartókonzol elektromos csatlakozókhoz
Könnyűszerkezetes konstrukció a repülőgépek belső terében: kompozitokon alapuló sorozatgyártású alkatrészek
A könnyű és nagy szilárdságú anyagok nélkülözhetetlenek a repülés high-end alkalmazásaihoz. Az utasszállító repülőgépeknél minden kilogramm számít, ezért a fémeket egyre inkább műanyag alapú megoldások váltják fel a belső térben. A hőre lágyuló kompozitok különösen a repülőgépek felszerelésével foglalkozó vállalatok számára kínálnak jelentős súlycsökkentést anélkül, hogy a mechanikai tulajdonságok tekintetében kompromisszumokat kellene kötniük. A Bucher Leichtbau és az Ensinger vállalatok projektje azt mutatja, hogy a szálerősítésű kompozitokra való áttérés további műszaki előnyökkel járhat.
A Bucher Leichtbau AG, amelynek székhelye Fällandenben (Svájc) található, repülőgép-belső terek és autóipari berendezések specialistája. A vállalatcsoport repülési részlege többek között utasszállító repülőgépek számára fejleszt és gyárt konyhákat és szekrényeket. Egy ilyen típusú teljes modul a saját súlyának nyolcszorosának megfelelő terhelést bír el, és legalább kilencszeres gravitációs gyorsulásnak kell ellenállnia. Itt különbséget kell tenni a repülési terhelések (normál repülési körülmények, például felszállás, leszállás, turbulencia) és a vészleszállási terhelések (ellenőrzött kényszerleszállás vagy megszakított felszállás) között. A gyártott modulok előírt minimális élettartama például az Airbus és a Boeing esetében 25 év.
Kiindulási helyzet: Anyag- és összeszerelési költségek
Biztonsági okokból a kereskedelmi repülésben az elektromos dugaszolható csatlakozók minden fémtartozékának földeltnek kell lennie. A Bucher alumíniumkonyhák elektromosan vezető tartószerkezeteinek esetében gyakran elegendő egy meglévő, a szükséges korrózióvédelmi intézkedésekkel ellátott rögzítőcsavar. Ha azonban a fémdugótartók a konyhák nem vezető szerkezetein helyezkednek el, az elektromos földeléshez további kábelre van szükség. Ezt a földelő kábelt rendszeres időközönként rögzíteni kell. Ehhez további rögzítőmenetekre, távtartó csavarokra, kábelbilincsekre, csavarokra stb. van szükség.
A kábel elvezetéshez szükséges anyagköltségeken kívül a tervezés és a telepítés is magas költségekkel jár: A tervezési munka magában foglalja egy bejegyzés elkészítését a kapcsolási rajzban; mi több, a vizsgálati tervben minden földelőkábelhez ellenállásmérést kell meghatározni. Ezt be kell építeni a vonatkozó karbantartási irányelvekbe és üzemeltetési utasításokba, valamint az engedélyezési dokumentumokba is. A gyártás során az érintkezési ellenállást fel kell jegyezni, és minden földelési csatlakozásnál korrózióvédő bevonatot kell alkalmazni.
A hőre lágyuló kompozitokból készült alkatrész feleslegessé teszi a földelést
A földeléssel járó extra munka és költségek teljesen kiküszöbölhetők, ha a korábban fémből készült csatlakozótartozékokat nem vezető változatra cserélik. Az üzemi hőmérséklet és a tűzvédelmi követelmények miatt azonban nem lehet olcsó, szabványos műanyagot használni.
A kívánt műszaki alternatívának alkalmasnak kellett lennie arra, hogy a meglévő alumíniumlemezből készült nagyszámú alkatrész egy az egyben kiváltható legyen, hogy a bevezetéskor a lehető legkevesebb munkával és költséggel járjon az átállás. Ahhoz, hogy ezt az igényt ki lehessen elégíteni, merev, nagy szilárdságú anyagra van szükség.
A különböző csatlakozótartozékok viszonylag kis darabszáma miatt a magas szerszámköltséggel járó megoldás nem jöhetett szóba. A szálerősítésű, hőre lágyuló műanyaglemezből készült, helyileg átalakított alkatrészekkel végzett kezdeti kísérletek nem mutattak kielégítő eredményeket az átmodellezett területeken.
Az Ensinger Composite részlegével együttműködve gyorsan találtak egy megfelelő megoldást hőre lágyuló, szálerősítésű kompozit alapanyagból. A repülőgépipar számára jóváhagyott, üvegszálas és PEI mátrixú (poliéterimid) prepreg anyagot választottak. Rövid optimalizálási fázis után lehetővé vált az első sorozatgyártású alkatrészek gyártása. A speciális gyártási technikák miatt az Ensinger két telephelye is részt vesz a csatlakozótartozékok gyártásában:
Az otelfingeni telephelyen az Ensinger kompozit szakértői a PEI prepregből szögletes alakú félkész alkatrészeket állítanak elő. A hasonló alkatrészekkel ellentétben ezeket az alapanyagokat nem vastag laminátumból vágják méretre és hőformázzák, hanem az egyes prepreg-rétegek felhasználásával egy szerszámban préselik a meghatározott formába. Ez az eljárás többek között azzal az előnnyel jár, hogy csökkenti a visszarugózási hatást. A szálkompozit alkatrészek CNC-megmunkálása a bajorországi Chamban található Ensinger GmbH-nál történik.
A chami megmunkáló részleg, amely hőre lágyuló, nagy teljesítményű műanyagokból és kompozit anyagokból készült precíziós alkatrészek gyártására specializálódott, az Ensinger nemzetközi forgácsoló csoportjának tagja. Az Otelfingenben gyártott szögletes nyersdarabokból az Ensinger Chamban megmunkálja a csatlakozótartozékokat a végső termékleírásnak megfelelően.
A legtöbb rögzítőkonzolnak több változata létezik, különböző méretekkel. A rugalmas eljárásnak köszönhetően a kontúrral vagy furatokkal ellátott speciális változatok is kiváló minőségben, gazdaságosan és rövid szállítási határidővel gyárthatók.
Egyszerűbb, költséghatékonyabb és könnyebb
CNC forgácsolás előtt
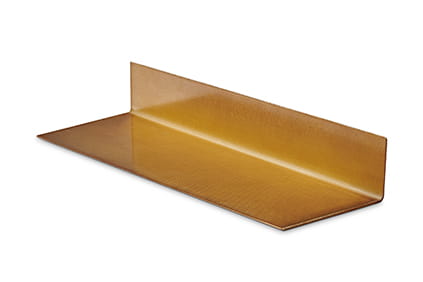
A csatlakozótartó alaplapja egy légiközlekedésre jóváhagyott PEI mátrixba ágyazott üvegszálakat tartalmazó kompozit prepregből készül.
A csatlakozótartók különböző méretű változatokban kaphatók. A folyamatos, irányított szálaknak köszönhetően a hőre lágyuló kompozit jelentősen nagyobb szilárdsággal és merevséggel rendelkezik, mint a rövid szálakkal erősített műanyagok.
PREFORM TECHNOLógia
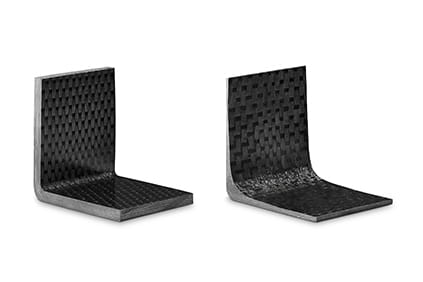
Az Ensinger előformázási technológiájának köszönhetően az idomok gyártásakor a falvastagságok közötti különbségek is lehetségesek. Így az ágvillához hasonlóan a nagy igénybevételnek kitett sarokrész megerősíthető, míg a nem nagy igénybevételnek kitett részeken (pl. a karokon) anyagot lehet megtakarítani. A gyártási technikát "near-to-shape" eljárásnak nevezik.
Az alkatrész geometriájától függően jelentős anyag- és tömegmegtakarítás érhető el ezzel a technológiával - hasonló szilárdság és merevség fenntartása mellett.