Retaining ring
A very important step in silicon wafer production is the Chemical Mechanical Planarization (CMP) process. The trend is towards larger wafer sizes, smaller chips with narrower line widths and feature sizes. The challenge is to find a material with the desired characteristics, as the CMP process requires components made of highly qualified materials. In close cooperation with customers, we have specialized in developing materials that meet these requirements.
Less processing errors due to higher stability
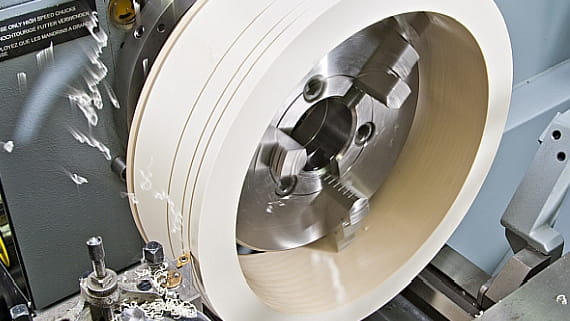
During the process of chemical mechanical planarization, the material comes into contact with different slurries, because the retaining ring has to hold the wafer during polishing. The slurries thus also have a negative effect on the handling components. The material also needs to withstand mechanical loads, so it should have good elasticity, toughness or strength.
Manufacturing retaining rings calls for a material that offers extreme processing precision and dimensional stability, in order to reduce the occurrence of microscratches in wafers and ensure a higher yield of usable ICs. The dimensional stability may be endangered by high mechanical loads, high temperatures or moisture.
Manufacturing retaining rings calls for a material that offers extreme processing precision and dimensional stability, in order to reduce the occurrence of microscratches in wafers and ensure a higher yield of usable ICs. The dimensional stability may be endangered by high mechanical loads, high temperatures or moisture.
High purity is very important throughout
the entire CMP process. Accordingly, the retaining ring also has to
have a high level of purity. This means that the material should not be contaminated by metals, such as aluminum or copper, to avoid scratches on the wafer surface. To prevent other damage to the wafer, the material of the retaining ring should have low outgassing properties.
Special applications require special materials
Usually, standard PPS is used for the retaining rings. PPS is a good choice in general, but there is still room for improvement. TECATRON CMP is a specially modified and improved material designed to meet the requirements of the CMP process, and explained below.
The PPS material TECATRON CMP is characterized by high abrasion and wear resistance, greater than twice the industry standard for PPS (see Chart 1). It has very good thermal and mechanical properties such as high tensile and flexural strength (see Chart 2), which is convenient when cleaning the wafer or during testing. In combination with chemical and solvent resistance, these tribological properties improve the service life of the plastic components.
Wear rate:
Strength:
TECAPEEK CMP can also meet the necessary requirements. This PEEK product is characterized by its toughness and high ductility, but also by its dimensional stability, due to which the shape remains stable.
Its excellent resistance to wear and abrasion is an advantage in the processes of CMP, deposition and testing. In combination with high chemical and temperature resistance, the mechanical and tribological properties, such as good elasticity (see Chart 3), ensure a significantly longer service life.
Modulus of elasticity:
Our high-performance plastics constantly meet or exceed the purity requirements and have been tested by industry-recognized laboratories on common metal materials to reduce the risk of metal contamination. In Chart 4 the low level of contamination of our materials can be seen in pollution in parts per million by material.
Retaining rings made of TECAPEEK CMP or TECATRON CMP have low outgassing, so that the wafer cannot be destroyed by emerging gases. Also, they are convenient in the processing stage of semi-finished products due to their improved machinability.
Contamination test:
Results/Benefits
The use of recommended materials leads to error reduction and extended lifetime of retaining rings. A greater number of wafers can thus be planarized before production is interrupted to change consumable sets in CMP production equipment. Furthermore, the costs per wafer fall because of reduced placement and downtimes. The benefits of these materials are already noticeable in the processing stage of the semi-finished products due to improved machinability, which allows short processing times and a minimal degree of deburring improves productivity.
Requirements can be as individual as the applications. Therefore we offer the following other materials:
- TECATRON SE (PPS): High dimensional stability and low creep tendency
- TECAPEEK SE (PEEK): Very good chemical resistance
- TECADUR PET CMP (PET): Good slide and wear properties